반도체 소자가 만들어지기까지의 과정을 살펴보겠습니다. 논리 설계를 하고 난 뒤 이를 회로 설계로 변환하고, 컴퓨터 지원 설계(Computer-Aided Design, CAD)를 통하여 마스크 패턴을 설계하여 마스크를 만들어냅니다. 그리고 실리콘 웨이퍼 위에 반도체를 만들어 가기 시작합니다.
즉, 모래로부터 실리콘 웨이퍼를 얻고, 웨이퍼 위에 증착과 패터닝, 식각, 불순물 첨가를 반복하면서 소자를 완성하죠. 웨이퍼로부터 소자를 만들기까지의 공정을 전공정(front-end process)이라고 합니다. 전공정을 마친 후에는 소자 테스트를 하고, 칩으로 잘라내고, 도선을 연결하고 패키징을 하죠. 패키징 후에는 다시 성능 평가를 하고 통과가 되면 마침내 후공정(back-end process)이 완료되고 이로써 우리가 컴퓨터나 휴대폰 안에서 볼 수 있는 반도체 부품들이 완성됩니다.
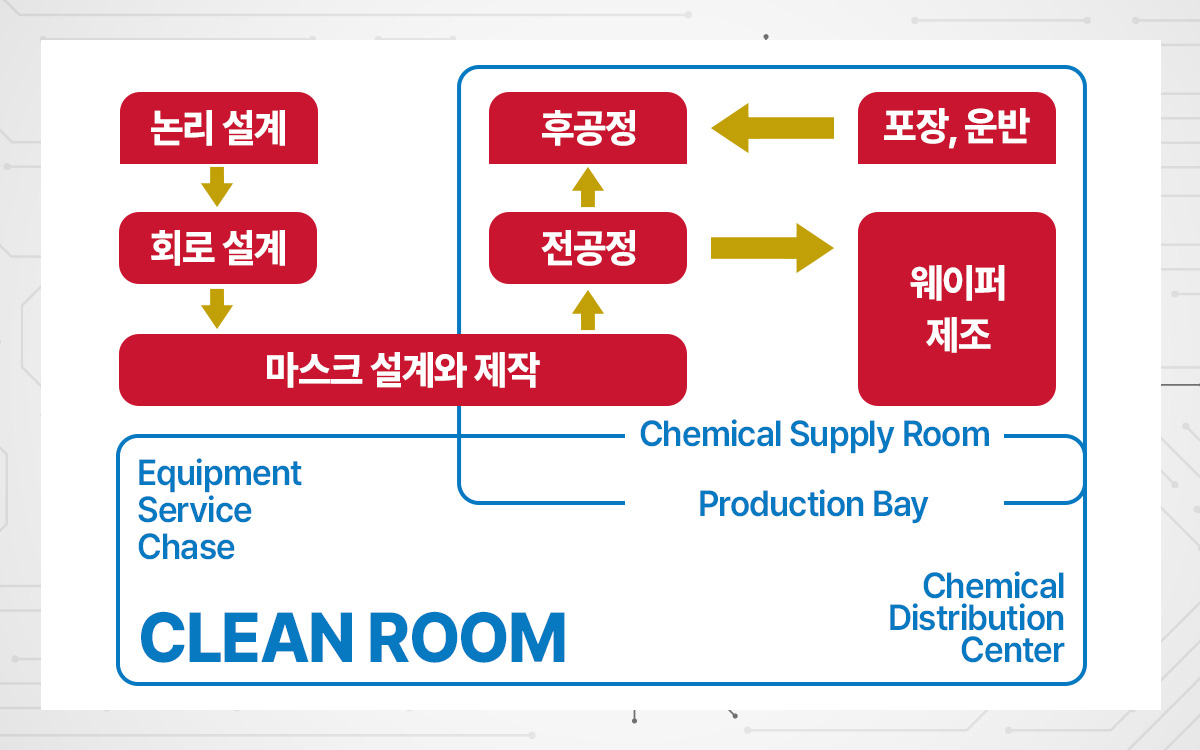
전공정을 비롯한 반도체 공정들은 기본적으로 청정실 안에서 진행이 됩니다. 공정이 이루어지는 동안에 작은 먼지 하나라도 웨이퍼 위에 내려앉게 되면 전기 배선들이 끊어지고 여러 개의 소자들이 망가지게 되죠. 청정실의 청정도는 ‘일정한 체적 안에서의 표준 크기 미립자의 수’로 표시됩니다. 1세제곱 피트(28.3 리터) 안에 0.5 미크론 이상의 미립자의 수로 나타내죠. 클래스 1,000은 미립자의 수가 천개 이하, 클래스 100은 백 개 이하입니다. 숫자가 줄어들수록 고청정 구역이라고 할 수 있습니다.
그리고, 청정실의 소자 제조 및 생산 공간에는 웨이퍼의 반입, 반출 공간 등 작업자가 실제로 필요로 하는 부분(production bay)만 설치되어 있고, 장비의 가동이나 유지를 위해 필요한 부분은 서비스 공간(equipment service chase), 장비 안으로 공급되는 화학 약품이나 가스 등은 공급실(chemical distribution & supply room)에 설치되어 있습니다.
작업 공간 안으로는 필터를 통하여 정화된 공기가 유입되며, 밖으로 나가는 방식으로 기류가 흐르고 있죠. 기류 방식에는 수직 및 수평 층류, 나류 및 혼류형, 그리고 터널형 등으로 다양하지만 필터층을 천장에 설치하고 위에서 아래로 기류가 움직이는 수직층류가 많이 사용됩니다.
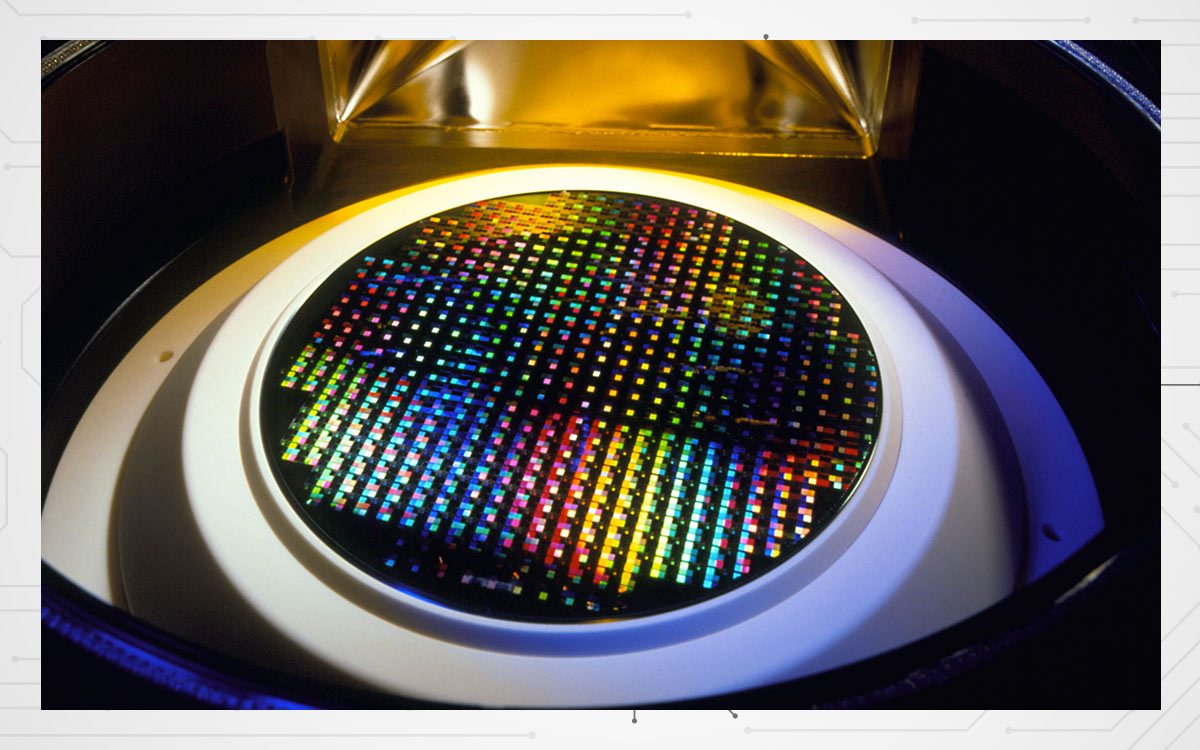
다음으로 실리콘 웨이퍼로 이야기를 이어갑니다. 마치 피자를 만들 때 도우 위에 토핑이 올라가듯이 집적회로는 웨이퍼(wafer)라는 얇은 기판 위에 만들어지죠. 웨이퍼는 반도체 결정을 성장시켜 만든 원형 기둥을 적당한 두께로 얇게 썬 원판을 의미합니다.
웨이퍼의 종류는 기반 물질에 따라 여러 가지가 있으며, 크게 실리콘 기반의 실리콘 웨이퍼와 비실리콘 웨이퍼로 구분됩니다. 그리고, 집적회로용 반도체 원소로는 실리콘(Si)을 모래에서 추출한 규소, 즉 실리콘(Si)이 가장 많이 사용되고 있습니다. 실리콘은 지구상에 풍부하게 존재하고 있어 안정적인 재료 수급이 가능하고, 독성이 없어 환경적으로도 우수하다는 장점 등을 가지기 때문이죠.
실리콘 웨이퍼를 성능이 낮은 순에서 높은 순으로 보면, 연마(polished) 웨이퍼→에피(epi, epitaxial) 웨이퍼→SOI(Silicon-On-Insulator) 웨이퍼 등으로 나열할 수 있습니다. 각각 반도체의 다양한 요구를 충족시키고 있죠. 물론 실리콘 웨이퍼는 형태적, 혹은 기능적으로 종류를 다양하게 분류가 되며, 광 소자나 광전 소자 등에 사용되는 비실리콘 웨이퍼는 이보다도 종류가 훨씬 더 많습니다.
실리콘 웨이퍼의 크기는 점점 더 증가하여 왔으며 2000년경에 등장한 직경 300mm의 웨이퍼가 주류를 이어가고 있습니다. 반도체 소자는 일괄 공정으로 제작되며 웨이퍼의 크기가 증가할수록 한 장의 웨이퍼 위에 동시에 만들어지는 칩의 수가 증가하죠.
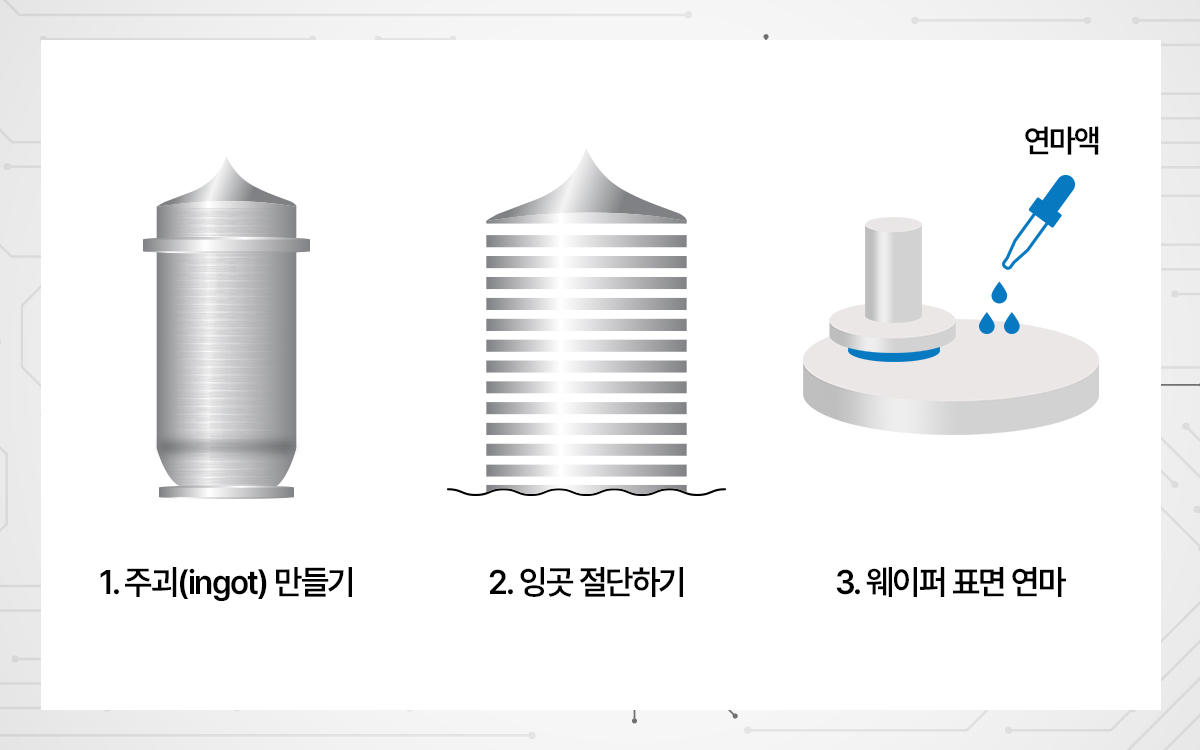
실리콘 웨이퍼는 모래로부터 실리콘 원소를 추출하여 만들며, 3단계의 공정을 거칩니다.
1단계는 주괴(ingot) 만들기입니다. 즉, 모래에서 추출한 실리콘을 반도체 재료로 사용하기 위해서는 순도를 높이는 정제 과정이 필요하죠. 실리콘 원료를 뜨거운 열로 녹여 고순도의 실리콘 용액을 만들고 이것을 결정 성장시켜 굳힙니다. 이렇게 만들어진 실리콘 기둥을 잉곳(ingot) 또는 주괴라고 합니다. 수 나노미터의 미세한 공정을 다루는 반도체용 잉곳은 실리콘 잉곳 중에서도 초고순도의 잉곳을 사용합니다.
2단계는 얇은 웨이퍼를 만들기 위해 잉곳 절단하기(wafer slicing)입니다. 원기둥 모양의 잉곳을 원판형의 웨이퍼로 만들기 위해서는 다이아몬드 톱을 이용해 균일한 두께로 얇게 써는 작업이 필요합니다. 잉곳의 지름이 웨이퍼의 크기를 결정하여 150mm(6인치), 200mm(8인치), 300mm(12인치) 등의 웨이퍼가 되죠. 웨이퍼 두께가 얇을수록 제조 원가가 줄어들며, 지름이 클수록 한 번에 생산할 수 있는 반도체 칩의 수가 증가하기 때문에 웨이퍼의 두께와 크기는 점차 얇고 커지는 추세입니다.
3단계는 웨이퍼 표면 연마하기(lapping & polishing)입니다. 절단된 웨이퍼는 가공을 거쳐 거울처럼 매끄럽게 만들어야 되죠. 절단 직후의 웨이퍼는 표면에 흠결이 있고 거칠어 회로의 정밀도에 영향을 미칠 수 있기 때문입니다. 그래서 연마액과 연마 장비를 통해 웨이퍼의 두께를 조절하고 표면을 매끄럽게 갈아냅니다.
자연에서의 모래는 주로 규암(quartzite)이며, 이는 규산염(silicate), 즉 실리콘과 산소가 결합한 물질이며 이산화규소(silica)가 주성분이죠. 이로부터 산소를 떼어내고 실리콘만을 추출합니다. 즉 이산화규소를 탄소 물질(SiC 등)과 함께 가열하면 일산화실리콘(SiO)과 일산화탄소(CO)가 기체가 되어 날아가고 실리콘만 남습니다. 이 실리콘에는 여전히 일부 불순물이 남아있으며, 여기에 염화수소를 넣어 반응을 시키면 수소 기체가 날아가고 실리콘은 염산에 녹아 액체가 됩니다. 이러한 액체, TCS(TriChloroSilane)에 열을 가하여 증발시켜 기체로 만들고 이를 수소와 반응시키면 염화수소 기체와 함께 고체 실리콘이 만들어집니다. 이 과정을 통하여 높은 순도의 다결정 실리콘 덩어리들을 얻을 수 있습니다.
이렇게 만들어진 고순도 다결정 실리콘은 단결정 실리콘을 얻기 위한 원료로 사용됩니다. 초크랄스키 방법을 통하여 단결정 실리콘 잉곳으로 태어나죠. 다결정들과 함께 3가 혹은 5가 불순물 첨가제(dopant) 원료를 도가니에 함께 넣고, 약 섭씨 1,500도의 온도에서 용융시킨 후, 작은 단결정 조각(seed)을 넣고 회전하면서 서서히 끌어올리면 원기둥 모양의 단결정 실리콘 잉곳이 만들어집니다.
만들어진 잉곳 모양은 양 끝이 뾰족한 원기둥 모양이며, 최초의 단결정(seed)으로부터 아래로 내려오면서 목(neck), 어깨(shoulder), 몸체(body), 그리고 원추형 끝단(end cone)으로 불립니다. 웨이퍼로 쓰이는 부분은 몸체가 되죠. 잉곳을 만드는 과정에서 실리콘의 결정 격자 방향은 용융된 실리콘에서 잉곳을 끌어올리는 작은 단결정(seed)의 결정 격자 방향을 따라서 액상에서 고상으로 변하는 실리콘 격자들이 줄을 서면서 결정됩니다. 즉, 잉곳의 결정성은 작은 단결정 하나로 정해집니다. 도핑 공정에서 실리콘 원자들의 격자 형태에 따라 침투하는 불순물 원소들의 움직임과 위치가 달라지며, 반도체 소자 내에서 전자의 움직임, 즉 이동도도 결정 방향에 영향을 받습니다.
잉곳의 몸체에는 성장 과정을 겪으면서 일부 불순물들이 포함됩니다. 이들을 일정량 이하로 감소시켜 웨이퍼의 순도를 높이기 위하여 정제(refining)를 하죠. 대역 정제법(zone refining)의 경우, 불순물을 포함한 물질이 용융 상태인 액체에서 고화할 때 고상 속에 포함되는 불순물의 농도가 액상 속에 포함되는 불순물의 농도보다 낮게 배분되는 편석(segregation)의 원리를 이용합니다. 즉, 용융 영역을 한쪽 끝에서 다른 쪽 끝으로 국부적으로 이동하여 가면서 불순물들을 액체 안으로 모이도록 하여 끝단으로 이동시키는 방법입니다. 횟수를 반복할수록 불순물들은 잉곳의 끝단에 쌓이게 되고, 원하는 순도가 얻어지면 끝단을 제거하고 사용하죠.
다만, 초크랄스키 성장에 이은 대역 정제법의 경우, 실리콘처럼 융점이 높고 용융 상태에서 화학적 활성이 큰 물질에서는 용기로부터의 오염이 문제가 될 수 있습니다. 이 경우 도가니나 보트를 사용하지 않는 성장 및 정제 방식인 부유대(Floating Zone, FZ) 방법이 있으나, 결정 반경의 방향으로 저항률 변화가 있는 약점 또한 존재합니다.
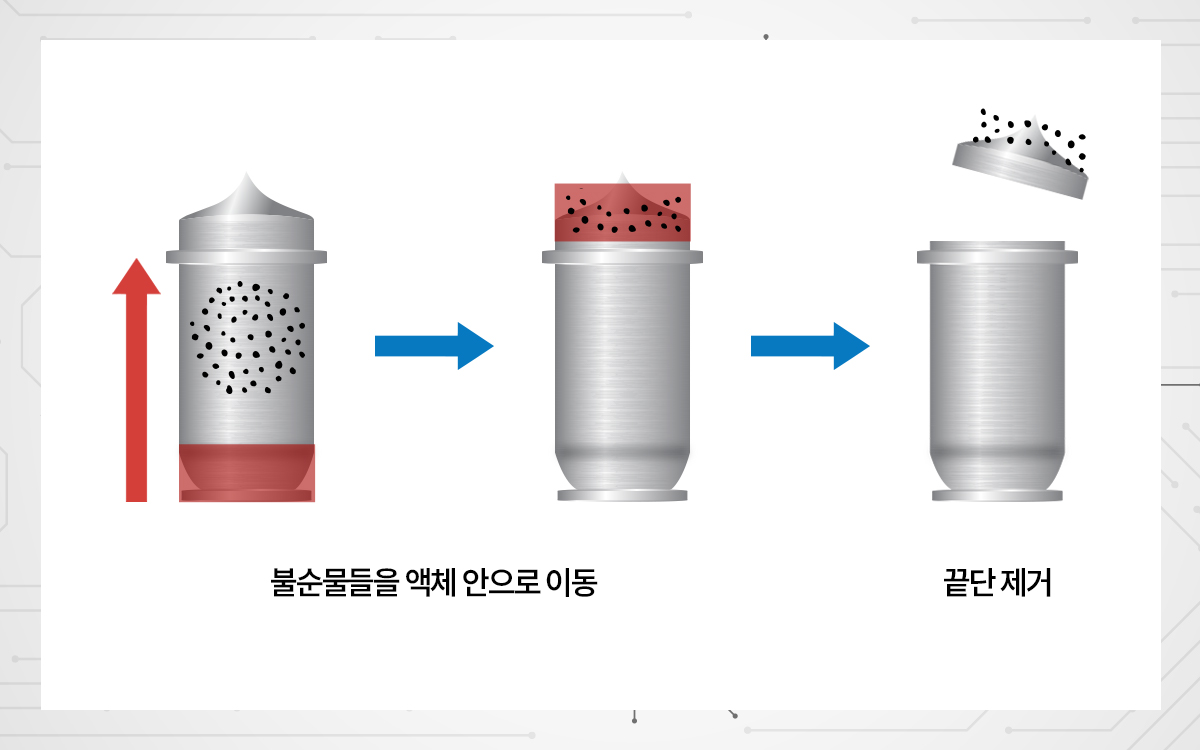
고순도로 얻어진 잉곳의 몸체 부분은 표면을 다듬고, 기준면을 만들고, 얇게 잘라내고, 표면을 연마하는 과정 등을 거쳐 최종 웨이퍼로 완성이 됩니다. 이상의 과정을 순서대로 표현하면 다음과 같습니다.
1) 고순도 다결정 실리콘을 석영 도가니에 채우는 공정(polysilicon stacking)
2) 다결정 실리콘을 고온으로 녹인 뒤 단결정 실리콘 잉곳으로 성장시키는 공정(ingot growing)
3) 잉곳의 표면을 매끄럽게 다듬은 뒤 블록 단위로 절단하는 공정(ingot grinding & cropping)
4) 잉곳 블록을 낱장의 웨이퍼로 절단하는 공정(ingot sawing)
5) 웨이퍼의 가장자리 형상을 가공하는 공정(edge grinding)
6) 웨이퍼의 표면을 매끄럽게 다듬고 평탄하게 만드는 공정(lapping)
7) 웨이퍼 표면의 가공 데미지를 화학작용을 이용해 제거하는 공정(etching)
8) 웨이퍼 표면의 작은 굴곡을 제거하는 공정(double side grinding)
9) 정밀 가공을 통해 웨이퍼 미세 굴곡을 제거하는 공정(polishing)
10) 웨이퍼 표면의 불순물을 제거하는 공정(cleaning)
11) 웨이퍼의 형상과 평탄도 등의 품질을 검사하는 공정(inspection)
12) 웨이퍼 표면의 결함을 검사하는 공정(particle counting)
13) 웨이퍼 위에 실리콘 단결정 층을 증착하는 공정(epitaxial growing)
14) 충격, 먼지, 습기로부터 보호하기 위해 제품을 포장하는 공정(packing)
이상의 과정을 통하여 실리콘 웨이퍼가 만들어지며, 웨이퍼의 전도 타입(n형, p형)과 결정성은 1차 및 2차 기준면(reference flat)을 참조로 알 수 있습니다.
완성된 연마 웨이퍼는 한쪽 면만을 연마한 것과 양면을 연마한 것으로 나뉘는데, 직경 12인치(300mm)부터는 단면보다는 양면 연마 웨이퍼가 주로 쓰이고 있습니다. 이렇게 생산된 연마 웨이퍼를 이용하여 성능이 좀 더 뛰어난 파생 웨이퍼들인 에피 웨이퍼나 SOI 웨이퍼 등들이 만들어집니다. 그리고, 얇은 두께의 웨이퍼가 필요하거나 일반적인 두께의 웨이퍼를 재생할 경우에도 연마를 하여 웨이퍼 두께를 감소시킵니다.
웨이퍼를 쓰임새별로 들여다보면, 프라임(prime) 웨이퍼, 테스트(test) 웨이퍼, 더미(dummy) 웨이퍼, 재생 웨이퍼 등이 있는데, 생산에 실질적으로 투입되는 웨이퍼는 프라임 웨이퍼입니다. 테스트 웨이퍼는 프라임 웨이퍼를 생산 라인에 투입하기 전에 공정의 이상 유무를 미리 점검하는 척후병 역할을 하고, 더미 웨이퍼는 공정에 프라임 웨이퍼와 같이 투입되기는 하지만 앞과 뒤에서 프라임 웨이퍼를 보호하는 역할을 하죠. 이렇게 만들어진 실리콘 웨이퍼 위에 반도체 전공정을 통하여 집적 회로칩을 만들고, 다음으로 후공정 과정을 거쳐 반도체 소자가 완성됩니다.
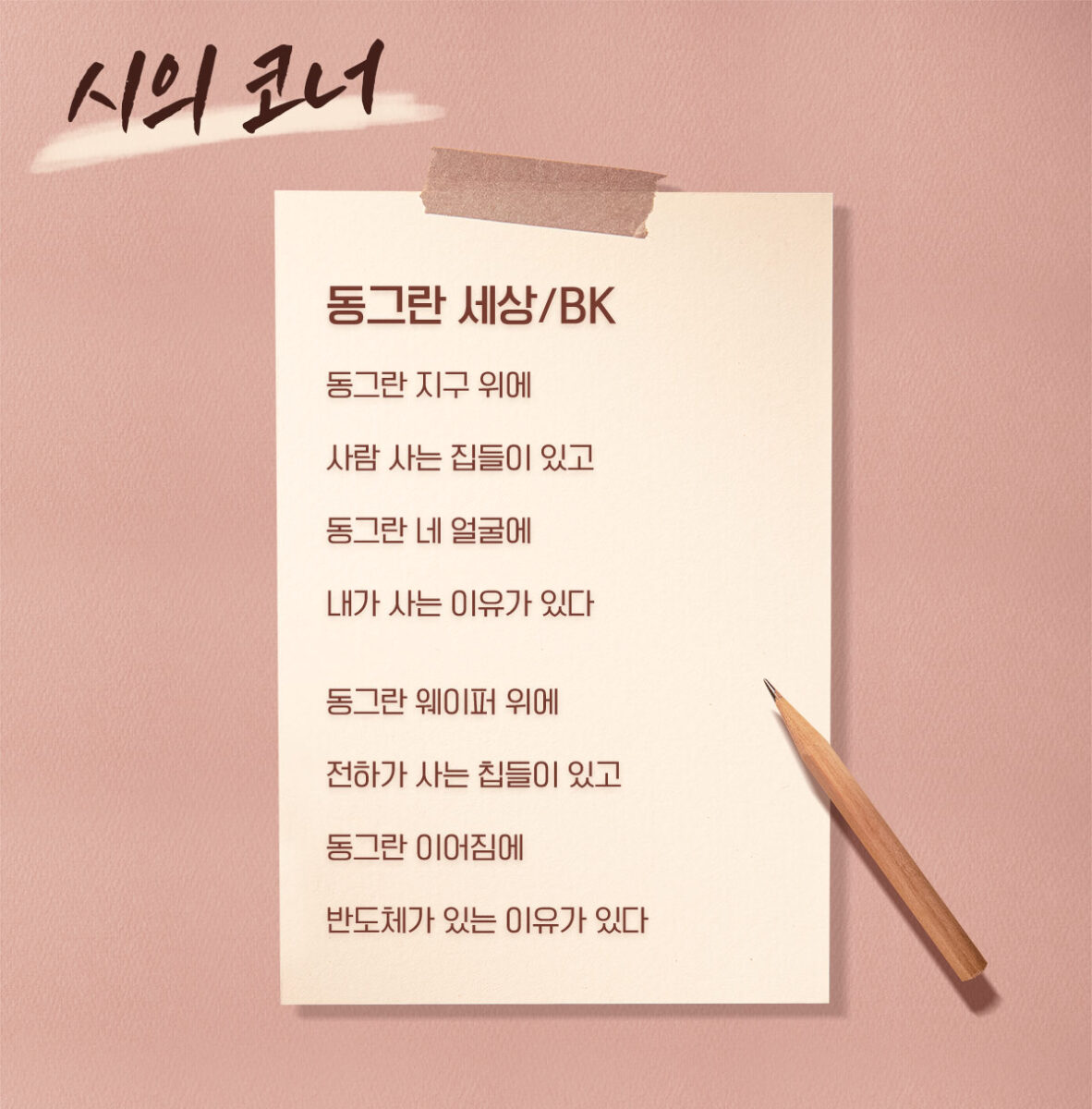
