반도체, 전공정
설계와 공정 개발이 완료가 되면 반도체 제조로 들어섭니다. 반도체 핵심 공정은 순서대로 웨이퍼 제조 공정, 산화 공정, 포토 공정(photolithography), 식각 공정, 증착 공정, 도핑(확산, 이온 주입) 공정, 금속 배선 공정, 웨이퍼 자동 선별(Electrical Die Sorting, EDS) 공정, 그리고 패키징 공정입니다. 여기에서 산화 공정부터 웨이퍼 자동 선별 공정까지를 전공정(frond-end process)이라 합니다. 즉, 웨이퍼 위에서 먼저 진행되는 공정이죠.
물론, 공정은 한쪽 방향으로만 진행되는 일방향 공정이 아니라, 설계하고, 마스크를 만들고, 공정을 진행하고, 그리고 공정 후 테스트를 통하여 성능 미흡이나 불량 시 다시 처음으로 돌아가기도 하고, 혹은 공정 과정에서 증착, 포토 공정 후 식각, 패터닝, 도핑 과정을 거쳐 증착 과정으로 돌아가기도 하는 폐루프로도 진행이 됩니다.
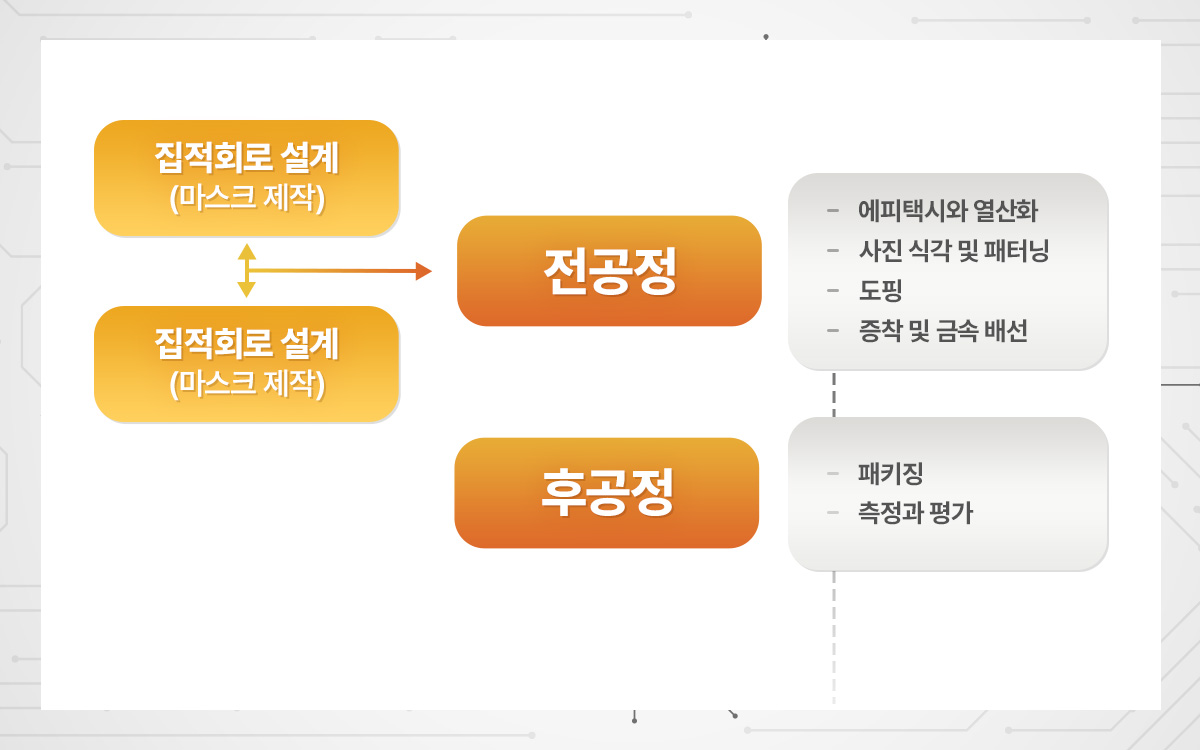
전공정에서 실리콘 웨이퍼 자체도 소모되는 막의 성장 공정인 단결정 실리콘층의 에피택시 공정과 열산화 공정을 묶어서 확산(diffusion), 즉 반응 원자들이 실리콘 기판의 내부로 확산하여 들어가는 공정으로 칭하기도 합니다. 그리고 포토 공정(photolithography)과 포토 공정 후 막의 식각 공정을 더하여서 사진 식각 공정이라고도 하죠. 증착 공정에 금속 배선 공정을 포함시키기도 합니다. 이러한 공정들을 통하여 웨이퍼 위에는 다이오드, MOSFET, CMOS 소자들과 이들의 집적회로가 제작됩니다.
반도체, 마스크 제작
반도체 공정에서 마스크(mask)는 사진 식각 공정에서 사용하며, 석영이나 유리와 같은 투명한 기판 위에 레이 아웃된 패턴들이 그려져 있습니다. 즉, 포토 공정마다 해당되는 마스크를 감광제가 코팅된 웨이퍼 위에 정렬하고 노광 후 현상, 식각을 하여 웨이퍼 위의 박막이나 구조들을 패터닝하죠. 이는 감광 물질이 도포된 기판에 패턴을 묘사할 수 있게 해준다는 점에서 사진의 필름과 유사한 역할을 한다고 볼 수 있습니다. 간단한 소자인 경우에는 몇 장 정도의 마스크로 만들어지지만, 회로가 복잡해질수록 마스크의 수도 증가하여 많게는 수십 장의 마스크들이 집적회로의 제작에 사용되고 있습니다.
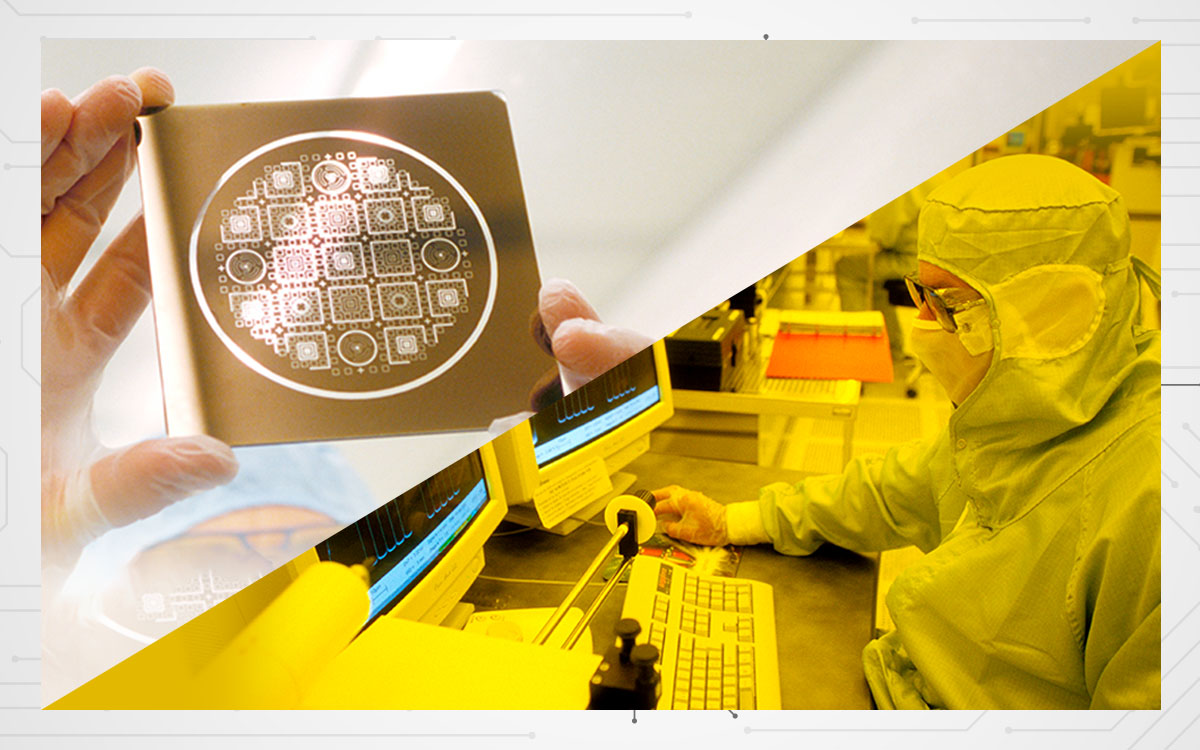
마스크를 제조하기 위해서는 먼저, 투명한 석영 기판에 크롬과 같은 금속 박막을 코팅하고 감광제를 도포한 뒤, 레이저 빔이나 전자선으로 CAD 패턴을 묘사하고 크롬을 선택적으로 식각, 제거하여 원하는 패턴을 형성합니다. 이를 바로 마스크로 사용할 수도 있지만, 일반적으로는 레티클로 사용하죠. 레티클은 실제 원하는 패턴보다 10배 정도 큰 패턴이 먼저 만들어진 판으로, 이를 10분의 1로 축소한 패턴을 마스크 기판 위에 반복적으로 전사하여서 마스크 원판을 만들어 가는 중간 과정입니다. 최종적으로는 웨이퍼 위에 만들고자 하는 패턴과 일대일로 대응되는 패턴이 형성된 마스크가 만들어지죠. 이와 같이 CAD 시스템으로부터의 데이터가 전자선의 움직임을 제어하면서 마스크 원판 위에 묘사하는 공정은 클래스 100 수준의 고청정, 노란색 조명 아래에서 이루어집니다. 노란색 빛은 감광제에 영향을 주지 않기 때문이죠.
반도체 전공정, 에피택시와 열산화
고온 전기로는 반도체 공정에서 기본이 되는 장비입니다. 고온 전기로 안에 웨이퍼를 넣고 온도를 올린 뒤 반응 기체들을 흘리면 에피택시, 열 산화, 증착, 확산, 열처리, 그리고 합금 공정 등, 다양한 공정들을 행할 수 있습니다. 특히 고온에서 이루어지는 공정이 에피택시와 열 산화입니다. 에피택시는 웨이퍼 위에 단결정층을 성장하는 공정입니다. 이 과정에서 웨이퍼 표면은 시드 결정(seed crystal)의 역할을 하며, 성장되는 결정은 웨이퍼와 같은 결정 구조와 방향성을 가지게 되죠. 실리콘 반도체 공정에서는 보통 전도 형태(type)나 전도도가 크게 다른 영역을 제공하기 위하여 사용됩니다. 이러한 에피택시 공정은 실리콘 웨이퍼 제조 업체로부터 수행되어 제공되는 경우도 많습니다.
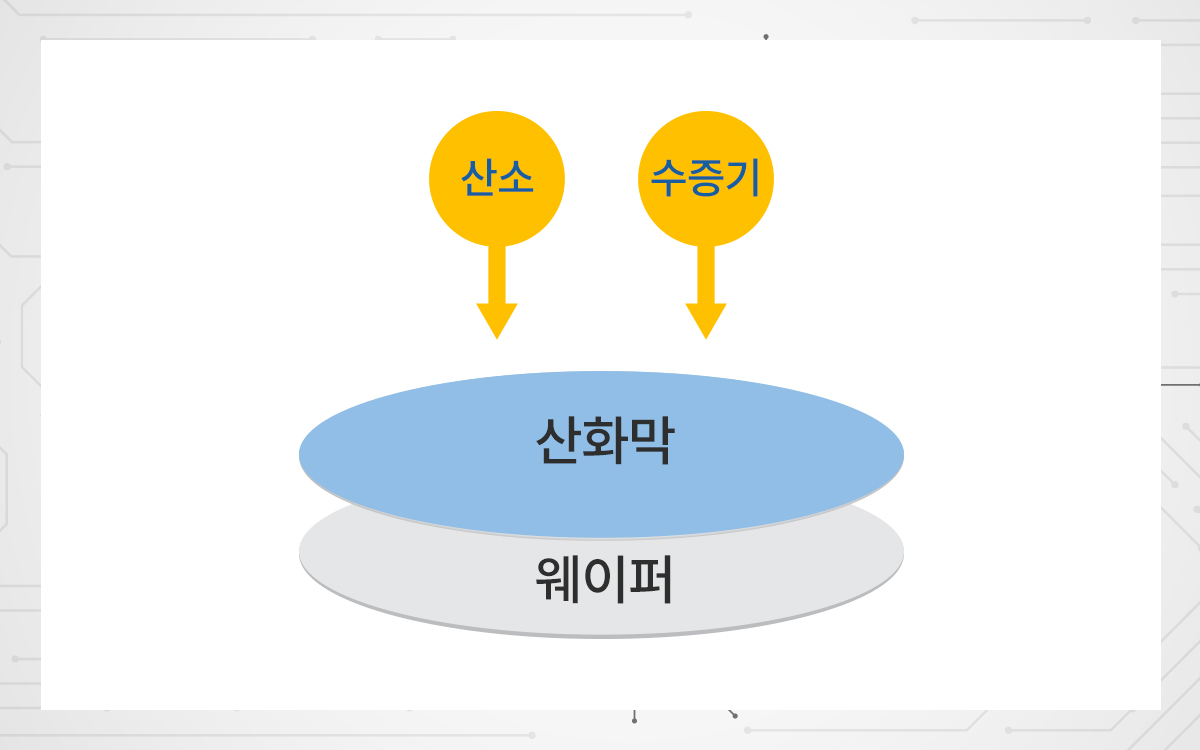
산화 공정을 거치는 이유는 웨이퍼에 절연막 역할을 하는 실리콘 산화막을 형성하여 회로와 회로 사이에 흐를 수 있는 누설 전류를 막기 위해서입니다. 산화막은 또한 식각 공정에서 특정 영역을 식각으로부터 보호하는 식각 방지막 역할, 도핑 공정에서 역시 일정 영역의 도핑을 막아주는 도핑 방지막 역할도 합니다. 특히, 양질의 산화막을 얻기 위해서는 낮은 온도에서 실리콘과 산소를 각각 함유한 기체들 간의 반응을 이용하는 증착(deposition)보다는 높은 온도에서 산소나 물분자가 실리콘 웨이퍼의 표면에 용해되어 내부로 확산되면서 실리콘 원자들과 반응을 하는 열 산화(thermal oxidation)가 더 효과적입니다.
예를 들어 열 산화막은 물 위에 얼음이 어는 경우이며, 증착은 얼음 위에 눈이 쌓이는 경우에 해당한다고 생각할 수 있습니다. 여기에서는 고온에서의 열 산화 공정을 설명합니다.
열 산화 공정은 대략 섭씨 800도에서 1,200도 정도의 범위에서 일어납니다. 이러한 고온의 전기로 안에 웨이퍼를 놓고 산소나 수증기를 흘려주면 이들이 실리콘 표면으로부터 내부로 용해, 그리고 확산이 일어나면서 실리콘 원자와 반응을 하여 실리콘 산화막이 성장됩니다.
산소를 이용한 경우를 건식 산화(dry oxidation), 수증기의 경우 습식 산화(wet oxidation)이라 하죠. 성장 속도는 느리지만 밀도가 높은 산화막을 필요로 하는 경우에는 건식 산화를 하고, 반면에 밀도는 다소 낮더라도 빠른 성장이 필요할 경우에는 습식 산화를 합니다. 이는 산소에 비해 수증기가 더 큰 용해도를 갖기 때문이죠. 그리고 성장된 열 산화막 두께의 45% 정도는 실리콘 웨이퍼를 잠식하면서 얻어집니다.
반도체 전공정, 사진 식각 및 패터닝
사진 식각 공정(photolithography & etching)은 감광막(photoresist)이 도포된 웨이퍼에 마스크를 정렬한 다음 자외선과 같은 빛 에너지를 조사하게 되면(exposure) 자외선에 노출된 감광막의 특성이 변하여 현상(development) 과정에서 선택적으로 패터닝이 됩니다. 다음 단계로 식각(etching)이나 도핑 과정이 진행되는데, 선택적으로 패터닝된 감광막에서 열린 부분에 대해 식각액이나 도핑용 불순물들이 들어갈 수 있어 웨이퍼의 선택적인 식각이나 도핑이 가능해지죠. 이는 마치 필름 사진을 찍을 때 필름 역할을 하는 마스크가 있고 이를 통하여 웨이퍼 위에 사진처럼 형상이 만들어지고, 이 형상을 이용하여 선택적인 식각 등이 일어난다고 하여 이러한 공정을 사진 식각 공정이라고 합니다.
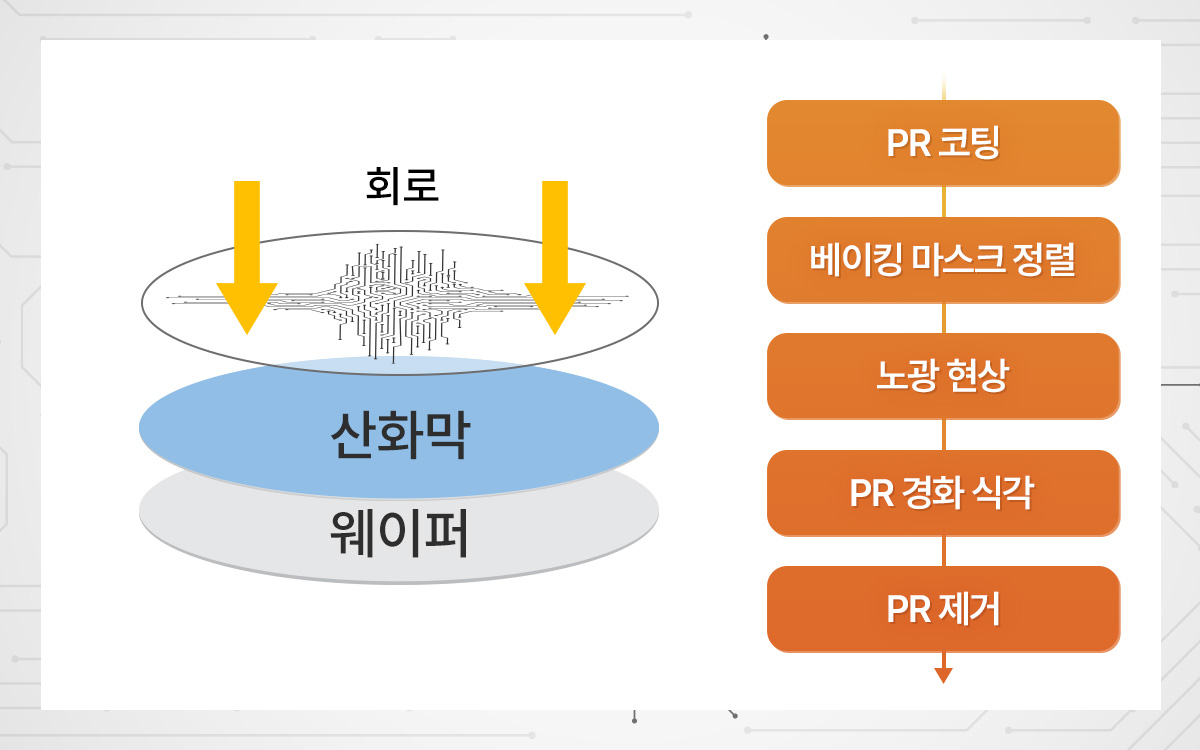
사진 식각 공정은 감광막이 영향을 받지 않는 노란색 조명의 청정실에서 행하여지며, 기본적으로 감광막 도포, 마스크 정렬, 자외선 조사, 현상, 감광막 경화, 그리고 식각 과정으로 진행됩니다. 감광막을 도포하는 방식은 기본적으로 스핀 코팅(spin coating)이 사용되나 이 외에도 분사 코팅(spray coating)이나 노즐을 이용한 슬롯 다이 코팅(slot die coating) 등이 있습니다. 그리고 마스크의 정렬 및 자외선 조사 방식에도 밀착(contact) 방식, 근접(proximity) 방식, 그리고 투사(projection) 방식이 있는데, 정밀도와 함께 패턴의 손상이나 마스크의 수명, 그리고 노광 장비의 성능과 가격 등을 고려하여 선택을 합니다. 감광제도 자외선 노출(exposure) 후 현상(development) 과정에서 노출 영역이 제거되면 양성(positive), 노출 영역이 남고 노출되지 않은 영역이 제거되면 음성(negative)으로 구분이 됩니다. 고분자 구조에서 보면 양성 감광제에서 제거되는 영역은 열경화성(thermoset)에서 열가소성(thermoplastic)으로 변화되며, 음성 감광제의 경우에는 반대로 되죠. 그리고 현상 과정을 통하여 패터닝된 감광막은 패턴 정밀도를 세밀하게 평가하여 다음 공정에서 문제가 없어야 합니다.
페터닝된 감광막에 열을 어느 정도 가하여 경화시킨 후 이를 식각 마스크(etching mask)로 하여 감광막 아래 물질에 대한 식각(etching)이 진행됩니다. 식각 공정은 용액과의 화학적 반응을 이용하는 습식 식각(wet etching)과 에너지가 큰 이온성 기체와의 물리적 충돌과 화학적 반응을 수반하는 건식 식각(dry etching)으로 구분됩니다. 습식 식각 방법에는 분사 혹은 분무(spray) 방식과 담금(immersion) 방식 등이 있으며, 건식 식각은 플라즈마나 반응성 이온 식각(Reactive Ion Etching, RIE) 또는 이온 밀링 등을 이용합니다.
습식 식각의 경우, 공정 장비와 가격 부담이 적고, 식각률이 높으며 물질에 따른 선택도가 우수한 반면, 미세 패턴 제작이 어렵고 용액 사용에 따른 위험성과 환경 유해성 면에서 불리합니다.
건식 식각은 미세 패턴 제작과 패턴 정밀도가 우수한 반면 장비 설치 비용이 상대적으로 높고 시간당 처리량(throughput)이 상대적으로 낮으며 선택도 그리고 전자기 방사에 의한 손상(radiation damage)에 관한 우려도 있죠.
반도체 전공정, 도핑
도핑(doping)은 절연체에 가까운 진성 반도체에 인위적으로 불순물을 넣어 전기 전도도를 높이는 과정입니다. 즉, 4가인 실리콘 안으로 5가인 비소(As)를 넣으면 자유전자가 만들어지고, 3가인 붕소(B)를 넣으면 정공이 만들어지죠. 이렇게 도핑을 하는 방법에는 높은 온도에서 불순물을 함유한 기체들이 실리콘 웨이퍼 안으로 녹아들어가서(용해), 농도 차이로 인하여 내부로 자연스럽게 이동하도록 하는 확산(diffusion)법이 있고, 에너지가 높은 원자(이온)들을 웨이퍼 표면을 관통, 내부로 반강제적으로 집어넣는 이온 주입(ion implantation)법이 있습니다.
확산 공정의 경우, 웨이퍼들이 배치된 고온의 전기로 안으로 불순물을 함유한 기체를 넣어 열분해된 불순물이 웨이퍼의 표면에 흡착되어 용해 과정을 거쳐 확산되도록 하는 방법이 있으며, 기체를 대신하여 고체 확산원을 웨이퍼와 마주 보도록 배치하는 방법도 있습니다. 기본적으로 웨이퍼의 표면에 불순물층이 형성되도록 하는 사전 증착(predeposition), 그리고 이렇게 형성된 불순물층으로부터 실리콘 내부로 불순물들이 용해 후 확산되도록 하는 재분포(redistribution) 두 개의 연속 과정으로 이루어집니다. 사전 증착 과정에서는 불순물이 무한하게 공급되며, 재분포 과정에서는 한정적인 양이 공급되죠. 이러한 차이와 공정 조건, 즉 온도와 시간 등을 설계, 조절하여서 웨이퍼 내에서 불순물 도핑 영역의 프로파일, 표면 저항과 접합 깊이 등을 결정합니다.
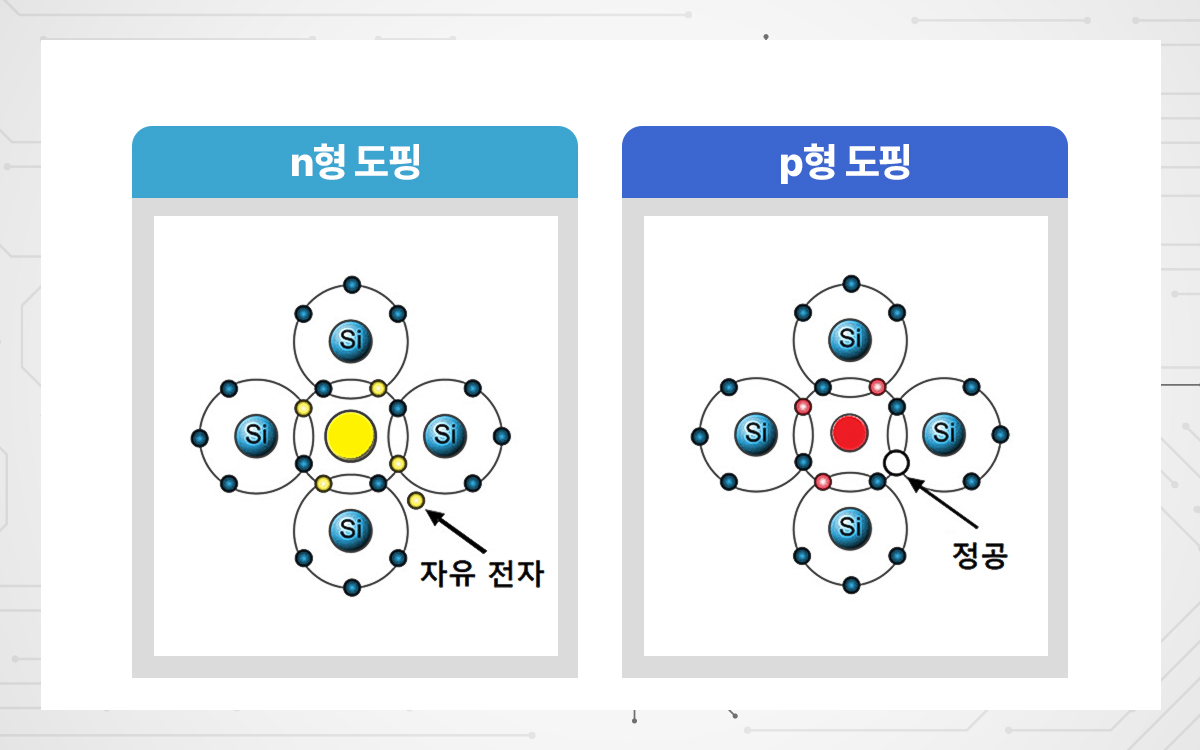
이온 주입 공정의 경우, 원자 또는 분자를 이온화하여 적절한 에너지로 가속시켜 웨이퍼 안쪽으로 원하는 깊이만큼 이르게 한 뒤, 열처리를 하는 과정입니다. 이온 주입 장치는 이온원(ion source), 이온 분리용 자석(ion exraction & seperation magnet), 빔 제어용 슬릿(beam control slit), 가속관(acceleration tube), 수직-수평 주사 장치(vertical-horizontal scanner), 공정 영역(process area)로 구성됩니다. 보통 가속 에너지는 20keV ~ 50MeV, 이로 인한 주입 깊이는 10nm ~ 수 마이크론까지 이르죠. 불순물의 농도와 도달하는 깊이는 주입량과 에너지로 결정을 하며, 주입된 불순물들이 지나가는 경로는 충돌 등으로 인하여 결정질이 파괴되어 거의 비정질 상태로 손상되므로 이를 복구하기 위한 열처리 과정이 수반되어야 합니다. 특징으로는 확산에 비하여 공정 시간이 짧고, 공정 온도도 낮으며(열처리 온도, 섭씨 900 ~ 1,000도), 도핑 수준의 조절 범위가 상대적으로 넓습니다.
반도체 전공정, 증착 및 금속 배선
증착, 특히 반도체 공정에서의 박막 증착(thin film deposition)은 웨이퍼 위에 얇은 막들을 만드는 과정입니다. 여기에는 단순한 물리적 충돌과 쌓임으로 진행되는 물리적 증착과 화학 반응을 수반하는 화학적 증착이 있죠. 물리적 증착법으로는 증착원에 열 에너지를 가하여 기체 상태로 만들어 웨이퍼에 이르게 한 뒤 온도를 낮춰 고체 상태의 막으로 돌아오게 하는 증발(evaporation)과 에너지를 가진 이온이 증착원과 충돌아여 이로부터 이탈된 원자들이 웨이퍼 표면으로 이동하여 쌓이게 하는 스퍼터링(sputtering)이 대표적입니다. 열 에너지는 저항 가열이나 혹은 전자선을 이용하여 제공되죠. 화학적 증착법으로는 서로 다른 기체들이 에너지를 얻어 화학 반응을 일으킴으로써 반응 생성물이 웨이퍼 위에서 막을 형성합니다. 이 때 반응 에너지원은 열이나 플라즈마 등을 사용하죠.
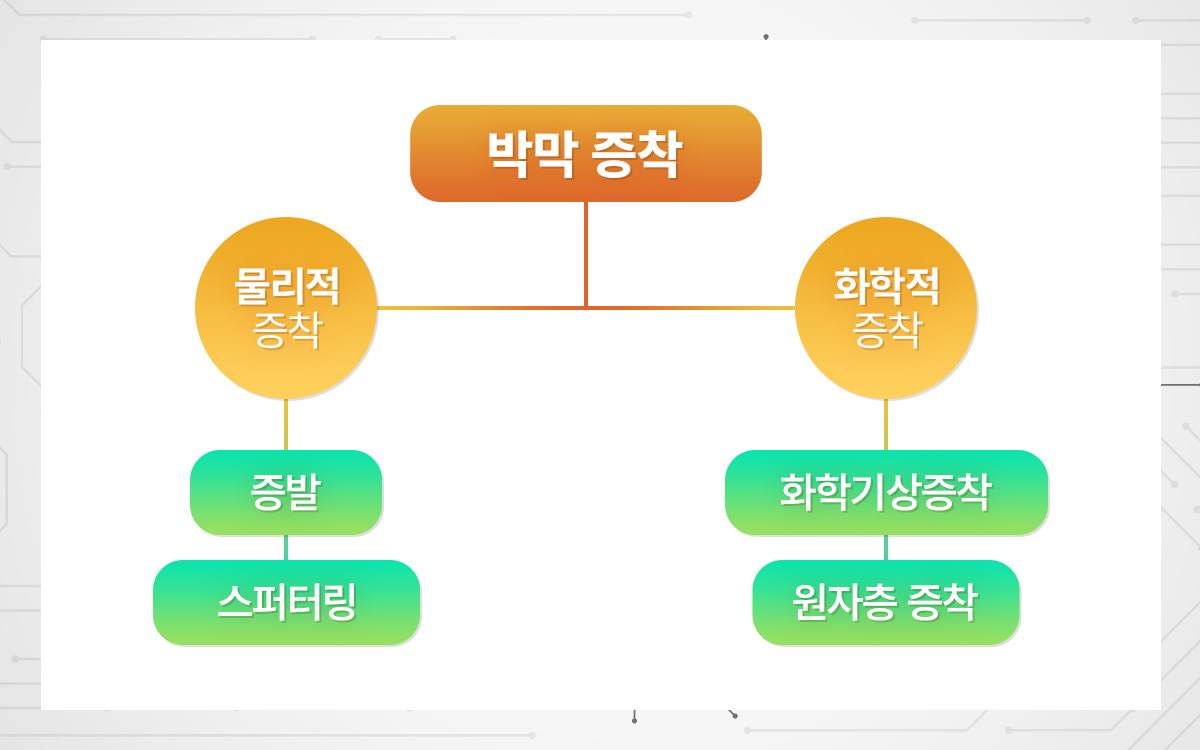
증발(evaporation)의 경우, 증발원을 보트에 넣고 보트나 필라멘트를 가열하여 증발원을 승화시켜서 웨이퍼에 박막을 형성하죠. 이 때 저항 가열 대신에 전자선을 사용하기도 합니다. 스퍼터링의 경우, 아르곤과 같은 이온들로 이루어진 플라즈마를 생성하고 이온들이 에너지를 얻어 타겟(증착원, target)과 물리적으로 충돌합니다. 충돌 과정에서 이탈된 타겟의 원자들이 웨이퍼 위에 쌓이면서 박막을 형성하죠.
화학적 증착인 화학 기상 증착(Chemical Vapor Deposition, CVD)에서는 기체들이 반응실로 들어오고(convection), 웨이퍼의 표면에 흡착되어(adsorption), 화학 반응을 하죠(reaction). 반응으로 만들어진 분자들은 표면에서 이동을 하면서(surface diffusion) 결합이 이루어지며 결정막을 만들어 갑니다(crystal film growth). 만들어지는 막은 주로 단결정 박막이지만 기판의 결정성이나 상태에 따라 다결정 박막이나 비정질막 등이 형성되기도 하죠. 반응에 참여하지 않은 기체들은 떨어져 나와(desorption) 외부로 배출됩니다(exhaust). 원자층 증착(Atomic Layer Deposition, ALD)은 반응 기체의 유입부터 반응 후 박막 생성, 그리고 잔류 기체의 배기를 사이클로하여, 한 사이클이 끝나면 다음 사이클이 시작되면서 원자층들을 차곡차곡 쌓아가는 방식으로 밀도가 높고 우수한 결정성을 갖는 막을 만들 수 있습니다.
화학 기상 증착에서 높은 공정 온도를 피하고 싶을 때는 반응을 위한 에너지로 열 대신 플라즈마를 사용합니다. 이러한 PE-CVD(Plasma-Enhanced CVD) 공정에서는 반응 기체들이 들어오면 이를 전기장으로 분리, 전구체(precursor)를 형성하여 웨이퍼에 흡착이 일어나도록 한 뒤, 전구체의 이동과 표면에서의 반응을 중심으로 막이 만들어집니다. 만들고자 하는 막의 종류와 증착 방식에 따라 다양한 반응 기체들이 사용되죠.
반도체 소자에서 전극으로 사용되는 금속 배선들도 이러한 박막 증착에 의해 막이 만들어지고, 다음으로 사진 식각 공정을 통하여 패터닝됩니다. 금속 전극용 증착 방식은 증발, 스퍼터링, 그리고 화학 기상법까지 다양하며, 이를 통하여 금속 혹은 합금이나 실리콘이 첨가된 금속 배선들이 제조됩니다.

